Industrial Box PCs - Driving Innovation in Robotics and Automation
6 examples of how robotics and automation are used in the manufacturing industry
The manufacturing industry continues to evolve thanks to the increased reliance on robotics and automation. As technology for robotic arms and collaborative robots improves, manufacturers can achieve better efficiency, precision and scalability. This fundamentally changes the design, assembly and delivery of products.
Content overview:
- AI Predictive Maintenance
- Automated Optical Inspection (AOI) for Quality Control
- Automated Visual Inspection (AVI) for Robotic Operation
- Robotic Arms
- Autonomous Mobile Robots (AMRs)
- Dimensioning, Weighing, and Scanning (DWS) Systems
AI Predictive Maintenance
AI predictive maintenance, also known as Predictive Failure Analysis (PFA), is an industrial automation method designed to detect problems with machinery. These systems are essential for ensuring optimal equipment performance and minimising downtime in manufacturing facilities.
Beyond simple failure detection, PFA can detect issues before they occur and predict when components will fail, providing essential information to reduce downtime and disruptions.
In Figure 1, an industrial box PC has been used for vibration monitoring of both screw and piston air compressors. Both rely on bearings to allow a low friction rotating motion; however, these bearings have a finite lifetime and will eventually fail.
A fanless box PC, is connected to single-axis smart vibration sensors to monitor vibrations from the compressors. It detects when these vibrations exceed user-set limits and uses a prediction model to estimate the remaining lifetime. Maintenance engineers can then monitor for problems and replace faulty machine components before failure. This helps maintain a smoothly run production process with minimal downtime.
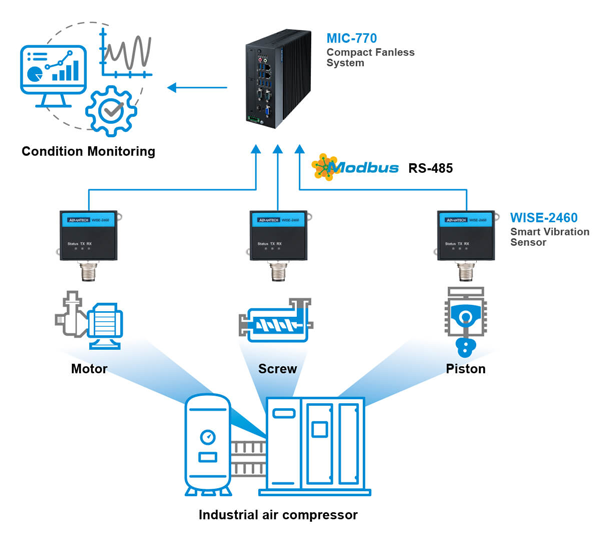
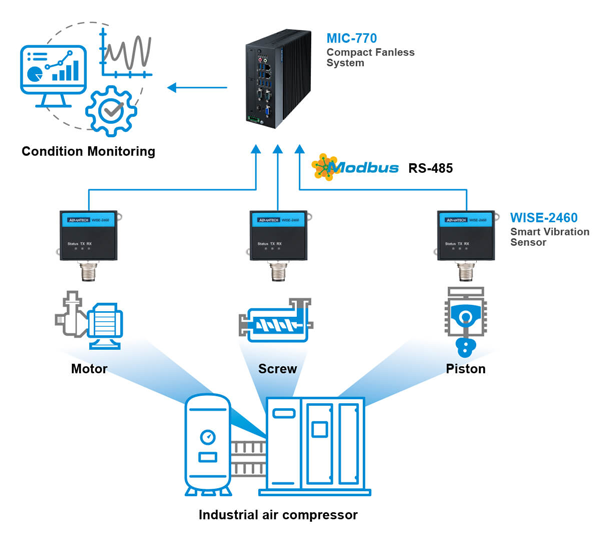
Figure 1.
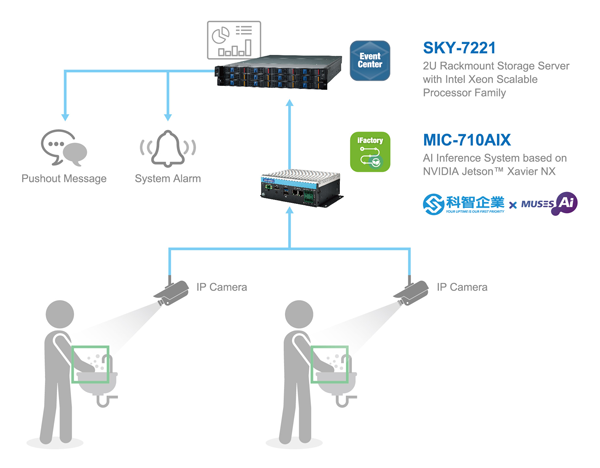
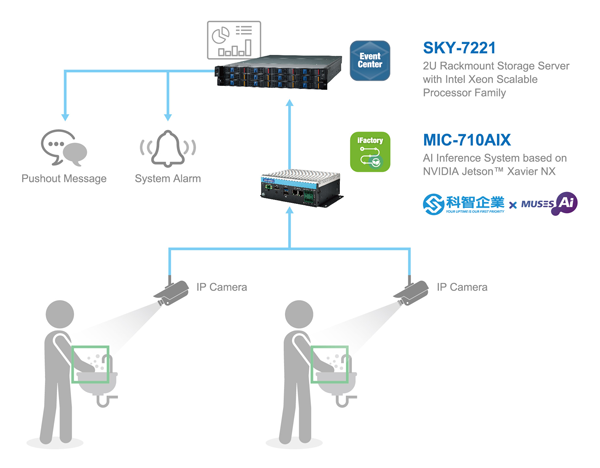
Automated Optical Inspection (AOI) for Quality Control
The development of factory robots has had a big impact on industries such as the food and beverage sector where it remains imperative for production line operatives to maintain a high standard of cleanliness when handling produce.
This is where IP cameras and industrial PCs can be used to monitor handwashing stations. In Figure 2, a capable box PC performs video analysis and records the resulting data, reporting to a central server. For multiple handwashing stations, several edge PCs can report into the central server.
The server can then raise an alarm or push messages as required to ensure the volume of produce with bacteria contamination is minimised, saving time and waste.
Figure 2.
Automated Visual Inspection (AVI) for Robotic Control and Guidance
Modern production lines use automated systems to increase output and reduce human error and labour costs in manufacturing processes. Some simple tasks can be accomplished knowing only when a component passes a certain position on a conveyor, however, we must use more advanced features to identify orientation and to track the trajectory of a moving object.
In one user case, Advantech implemented a mid-sized box PC chassis and Micro-ATX industrial motherboard for a client who required high performance, high core count computing with PCIe, USB, and Ethernet expansion options for an additional GPU, high-speed cameras, image capture, and control of a robotic arm.
In Figure 3, cameras capture the environment in real-time, the GPU processes this information to perform the required inspection, and the CPU instructs the robot to perform and corrective action. Using calibrated cameras, we can also perform pose estimation of components to guide the robot along the same trajectory.
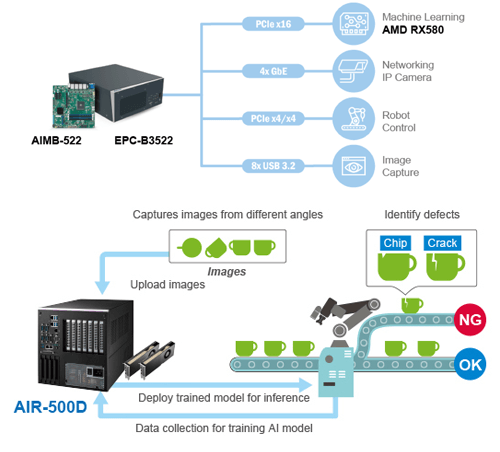
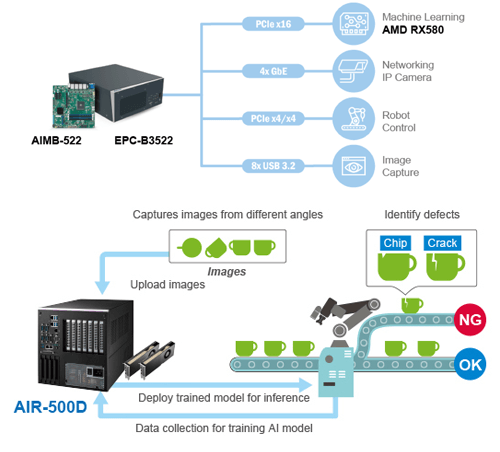
Figure 3.
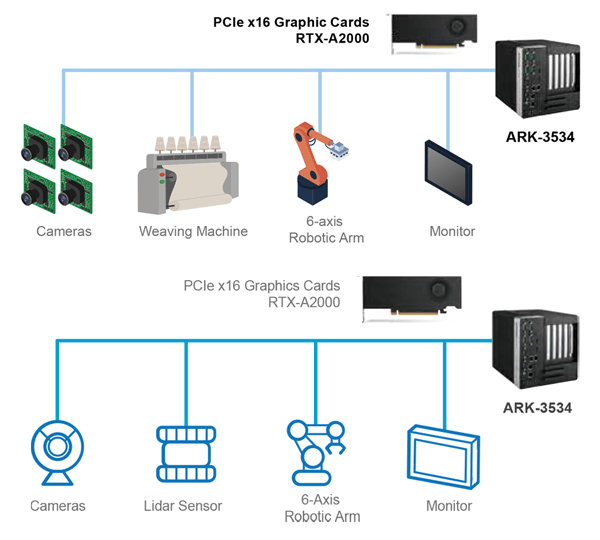
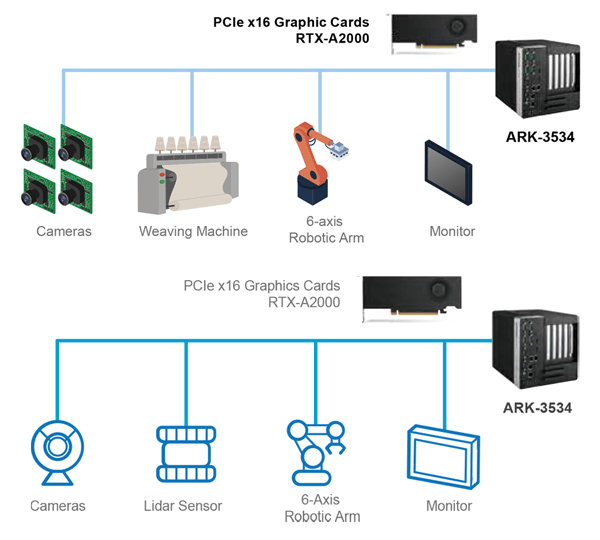
Industrial Robotic Arms
An industrial robotic arm, sometimes referred to as a collaborative robot (or cobot), is a robotic application designed to safely operate alongside humans in a shared workspace. Typically, these robots are used in assembly lines - none more so than in the automotive industry.
Robotic arms have been utilised to dynamically and efficiently move products through production facilities, perform roles considered dangerous for people, and enable a more autonomous world. Figure 4 shows an Advantech ARK-3534 implemented in a weaving machine and robotic fruit harvester. The Advantech ARK-3534 meets diverse automation requirements with its array of interfaces and is aimed at AOI and automation applications.
Comprising of up to 25 input and output connections (including up to 2x PCI, 1x PCIe x16 and 1x PCIe x4) it can support data acquisition cards, image/video capture cards, communication interfaces and GPUs to facilitate image processing, motion control, AOI and AI acceleration simultaneously. With the PCI interface, it is also a great choice for legacy applications.
These types of robotic arms help address labour shortages, increase productivity, and assist with manufacturing consistency and quality control.
Figure 4.
Autonomous Mobile Robots (AMRs)
AMRs are being used more frequently in factory automation delivery systems. Performing pallet/storage box movements smartly and in parallel with other AMR systems, they can be used to increase output, reduce human error and cut labour costs in manufacturing processes.
These AMR’s need to have an awareness of their surroundings (fixed objects, other AMRs, and human movements) to avoid collisions. This is usually facilitated by cameras and Light Detection and Ranging (LIDAR) in combination with a detection model.
There also needs to be a reliable, low-latency network in the AMR environment to enable time sensitive communications and accurate movements. Advantech manufactures both 5G and Wi-Fi wireless modules to an industrial grade. These can be built into AMR embedded computing solutions to provide access to the fixed network.
5G users can benefit from much more consistent latency, improved security and better coverage, whereas Wi-Fi users can benefit from ease of implementation and lower costs.
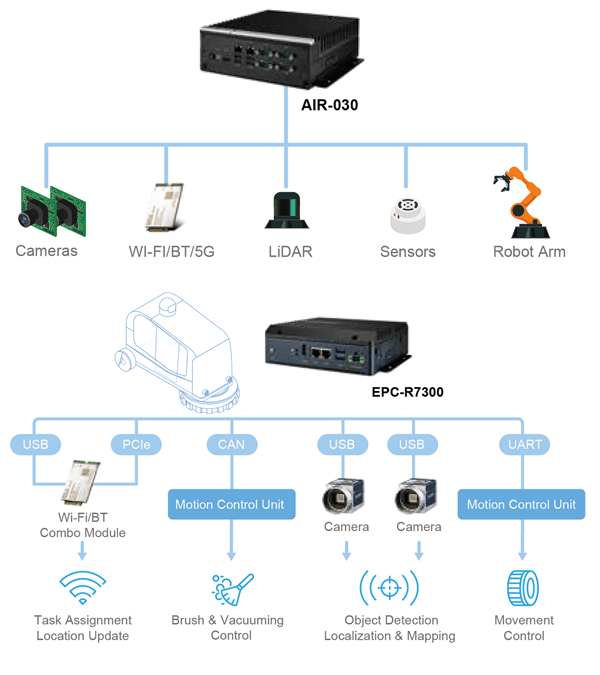
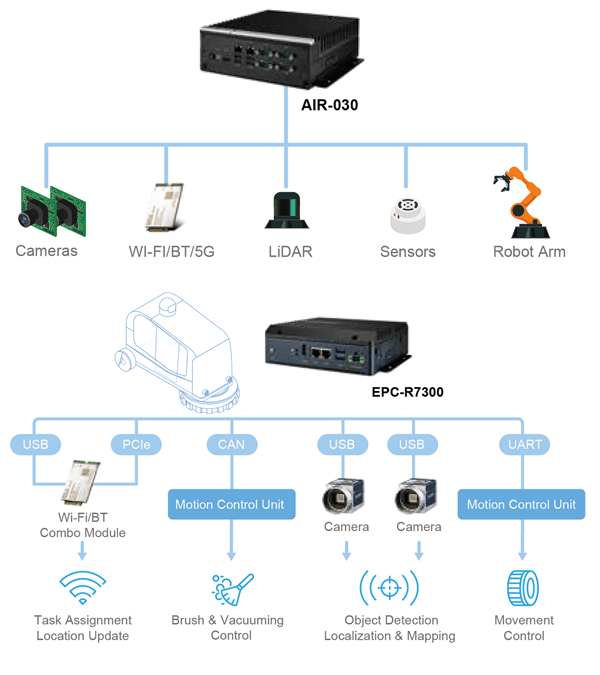
Figure 5.
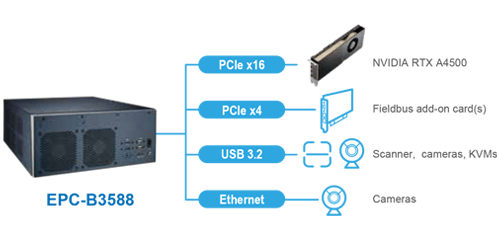
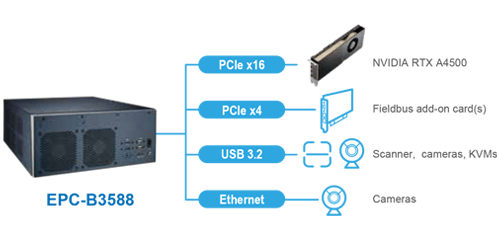
Dimensioning, Weighing, and Scanning (DWS) Systems
With the ever-growing demand for next-day delivery and the proposal of last-mile delivery solutions, warehouses and production lines are implementing DWS systems to speed up the packaging and identification process.
Figure 6 shows how Advantech’s box PCs have been used in conjunction with IP cameras to identify barcodes and handwritten text, a scale for weighing, and optical sensors for capturing the dimensions.
The software on the PC can digitalise handwriting and recognise many types of shipping label formats, even if the information is damaged, misplaced or unclear. This example leverages four PCIe x16 slots for Nvidia-certified GPU-accelerated computing and fieldbus cards.
Figure 6.
Why Advantech’s Industrial Box PCs are the Right Choice for your Next Robotics and Automation Project
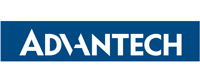
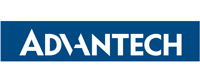
Advantech offers a comprehensive market-leading range of Edge AI and industrial box PC solutions to meet the diverse needs of modern factories. Edge AI is revolutionising factory operations by integrating advanced AI capabilities into edge devices and reducing the latency compared to processing raw data on a central server. This technology not only improves efficiency and accuracy but also automates production processes, making factories smarter and more flexible.
Advantech’s solutions offer:
- Exceptional performance in industrial manufacturing environments – rugged design, wide operating temperatures, vibration tolerance, and IP rating for water and dust ingress protection.
- Product longevity with on-going support – suitable for projects with long design-in requirements.
- High flexibility and easy expansion capabilities with a full range product offering of industrial memory, storage and wireless solutions.
- Integration services including SCADA, HMI, CNC and AOI software, wireless connectivity, and certification.
- DeviceOn software to remotely control hardware, perform over-the-air (OTA) updates, and collect inference results – functions which are helpful when deploying AI at the edge.
- Supported pricing and expert support with product customisation from APC such as custom BIOS and artwork.
Expert advice and support with your industrial robotic and automation applications
APC are a long-standing Advantech Premium Channel Partner in the UK and Ireland, working closely together for over 19 years.
We offer the latest x86 and RISC-based embedded technology and value-added software that customers can integrate into their application. Our in-house team of experts can advise and support on Advantech’s comprehensive range of embedded boards and systems, reassuring customers that solutions are compatible and have the necessary longevity for their projects.
Key overview of Advantech solutions for Robotics and Automation
AI Predictive Maintenance:
Monitor equipment health and predict equipment failure with Advantech’s MIC-770 Compact Fanless Industrial PC, used in conjunction with WISE-2460.
Automated Optical Inspection:
Ensure product quality and consistency. Advantech’s MIC-710AIX (with NVIDIA® Jetson™ Xavier NX module) implemented with the SKY-7221 central server enables the integration of high-resolution cameras and AI algorithms to perform real-time monitoring.
Robotic Arms:
Automate tasks and improve productivity with Advantech’s ARK-3534.
Automated Visual Inspection (AVI):
Automate warehouse operations and improve productivity with a range of Advantech AI Interface Systems based on NVIDIA Jetson.
Dimensioning, Weighing, and Scanning:
Optimise packaging and identification processes.
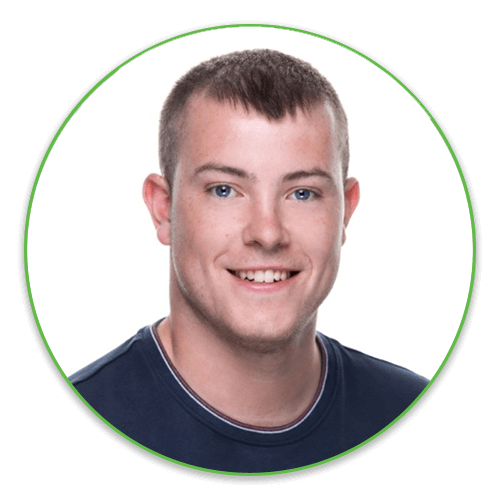
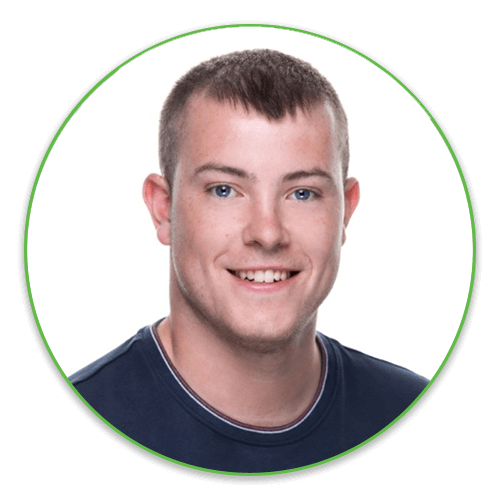
About the Author
Harry Aryton, MEng MIET
Field Application Engineer at APC Technology Group
As a member of our System division at APC Technology Group, Harry Aryton is an expert in the field of embedded/industrial computing and automated systems, Defence-grade computing and Secure private 5G networking for the edge for use in critical applications in military, medical, electric vehicle, and 5G market segments.
Contact us
Contact our expert embedded computing team for technical advice and pricing support for your robotics and automation projects.