Motor Controls in Space: Advanced Solutions from Vorago Technologies
- APC Technology Group
- Insights & Events
- 11 Apr 2025

Ensuring Reliable Motor Control in Space: The Role of Radiation-Hardened Microcontrollers
The reliable operation of motors is essential for space missions. Motors are used in spacecraft, satellites, and rovers to power components like robotic arms, landing gear, reaction wheels, solar arrays, and scientific instruments. Space is a harsh environment, particularly due to radiation, and specialised electronics, such as radiation-hardened microcontrollers, are required to ensure consistent, error-free motor function.
Motor Control in Space
Motor control systems are vital for spacecraft, powering key components.
Motors in space missions are used for:
- Satellite Operations: Adjusting antenna orientations, deploying solar panels, and controlling mechanisms like reaction wheels for attitude adjustments.
- Solar Array Positioning: Adjusting the angle for optimal energy generation.
- Robotic Arms: Assisting with object manipulation and sample collection on the ISS and rovers.
- Wheel and Track Movement: Enabling planetary rovers, like those on Mars, to traverse uneven terrain.
Motor control in space typically uses stepper and DC motors, with feedback mechanisms to adjust speed, position, and torque. To overcome the challenges and ensure reliable motor control operation, Vorago designs and manufactures radiation-hardened microcontrollers specially designed to withstand the harsh environment of space.
Motor Type | Advantages | Disadvantages | Common Applications |
---|---|---|---|
Stepper Motor | Precise position control, does not require closed-loop feedback, high reliability | Power consumption can be high, lower efficiency compared to BLDC | Antenna pointing, scientific instrument positioning, camera gimbal systems |
Brushless DC (BLDC) Motor | High efficiency, long lifespan, minimal maintenance, smooth operation | Requires electronic commutation, more complex control system | Reaction wheels, robotic actuators, satellite stabilization, propulsion valves |
Brushed DC Motor | Simple control system, low cost, good for short-term missions | Brush wear leads to shorter lifespan, not ideal for long-term missions | Short-duration missions, low-cost satellite mechanisms, simple actuation tasks |
Harmonic Drive System | High torque-to-weight ratio, zero backlash, excellent for robotic applications | More complex and expensive, requires precise manufacturing | Robotic arms, solar array deployment, precision instrument movement |
Voice Coil Actuator | Highly precise linear motion, no mechanical wear, ideal for fine adjustments | Limited range of motion, low force output compared to rotary motors | Optical instrument fine-tuning, mirror positioning, focus adjustments |
Understanding the Challenges of Space Radiation
Spacecraft must operate in high radiation environments, with cosmic rays, solar particles, and trapped particles in the Van Allen radiation belts all posing significant risks.
These radiation levels can lead to:
- Single Event Upsets (SEUs): High-energy particles can cause bit flips, disrupting data and instructions.
- Latch-up: Charged particles can cause integrated circuits to conduct too much current, leading to failure or burnout.
- Total Ionizing Dose (TID): Over time, radiation exposure degrades electronic materials, risking malfunction or failure
These issues can lead to mission-critical failures in motor control systems, such as robotic arm malfunctions or rover immobility. Reliable electronics are essential for ensuring consistent motor function in space.
Radiation-Hardened Microcontrollers: A Solution for Space Motor Controls
Radiation-hardened microcontrollers are designed to withstand these challenges. They mitigate SEUs, latch-up, and TID effects, ensuring reliable motor control in space.
Key features include:
- SEU and Latch-up Mitigation: Hardened memory and circuits, along with techniques like Triple Modular Redundancy (TMR), reduce the risk of errors and system failure.
- Enhanced TID Tolerance: Special materials and designs ensure long-term functionality, even with prolonged exposure to space radiation.
- Redundancy and Fault-Tolerance: Error-correcting codes and watchdog timers ensure systems stay operational even if a component is affected by radiation. These microcontrollers are essential for controlling motors in space, where precision and reliability are vital for mission success.
Applications of Radiation-Hardened Motor Controls with APC
Radiation-hardened microcontrollers are crucial in various space missions, including:
- Mars Rovers: Managing movement, robotic arm positioning, and instrument adjustments.
- Space Telescopes and Satellites: Controlling the orientation of mirrors and instruments.
- Deep-Space Probes: Ensuring long-duration communication and orientation adjustments.
VORAGO MCUs for Motor Control - Available with Expert Advice From APC Technology Group
In space applications, choosing the right processing hardware is essential to balance performance, cost, and development time. Radiation-hardened microcontrollers (MCUs), such as VORAGO Technologies’ VA41630, provide a cost-effective and efficient solution for key motor control tasks.
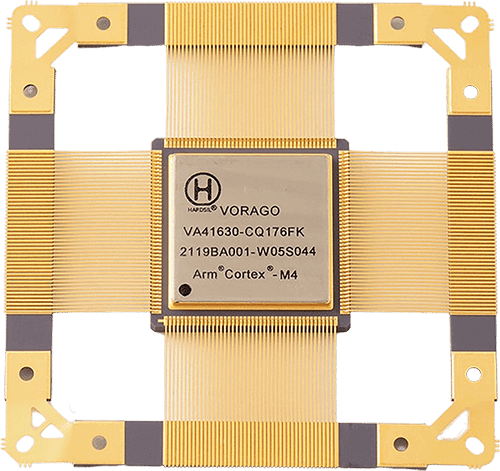
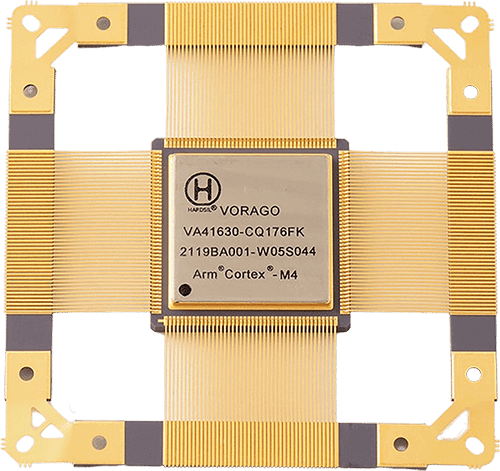
These MCUs support rapid prototyping, enabling engineers to carry out design iterations in minutes rather than the hours or days typically needed with Field Programmable Gate Arrays (FPGAs). FPGAs remain a strong choice for applications requiring high power or multiple implementations.
However, in many space scenarios, such performance is not necessary. Radiation-hardened MCUs offer a more suitable price-to-performance ratio for controlling antennas, reaction wheels, instrument interfaces, and robotic arms. They also allow for more direct access to control settings and can reduce CPU load by offloading key functions from software to hardware.
The VA41630, for example, is a radiation-hardened Arm® Cortex®-M4 microcontroller with 256kB of program memory, 64kB of data memory, an 8-channel ADC, a 2-channel DAC, and interfaces such as Ethernet and SpaceWire. Its reliability and performance make it an excellent fit for space-based motor control.
When it comes to selecting and designing in high-quality, radiation-hardened microcontrollers like VORAGO’s solutions, APC Technology Group offers a wealth of knowledge and technical expertise. With a long and successful heritage supporting projects in the space sector, our technical team provide reliable, cutting-edge technologies tailored to meet the specific needs of demanding space environments.
VORAGO's Radiation Hardened Microcontroller Solutions are
available at APC Technology Group