Rad-hard vs. Rad-tolerant - find out more about VORAGO Technologies solutions
- APC Technology Group
- Articles
- 12 Jan 2024
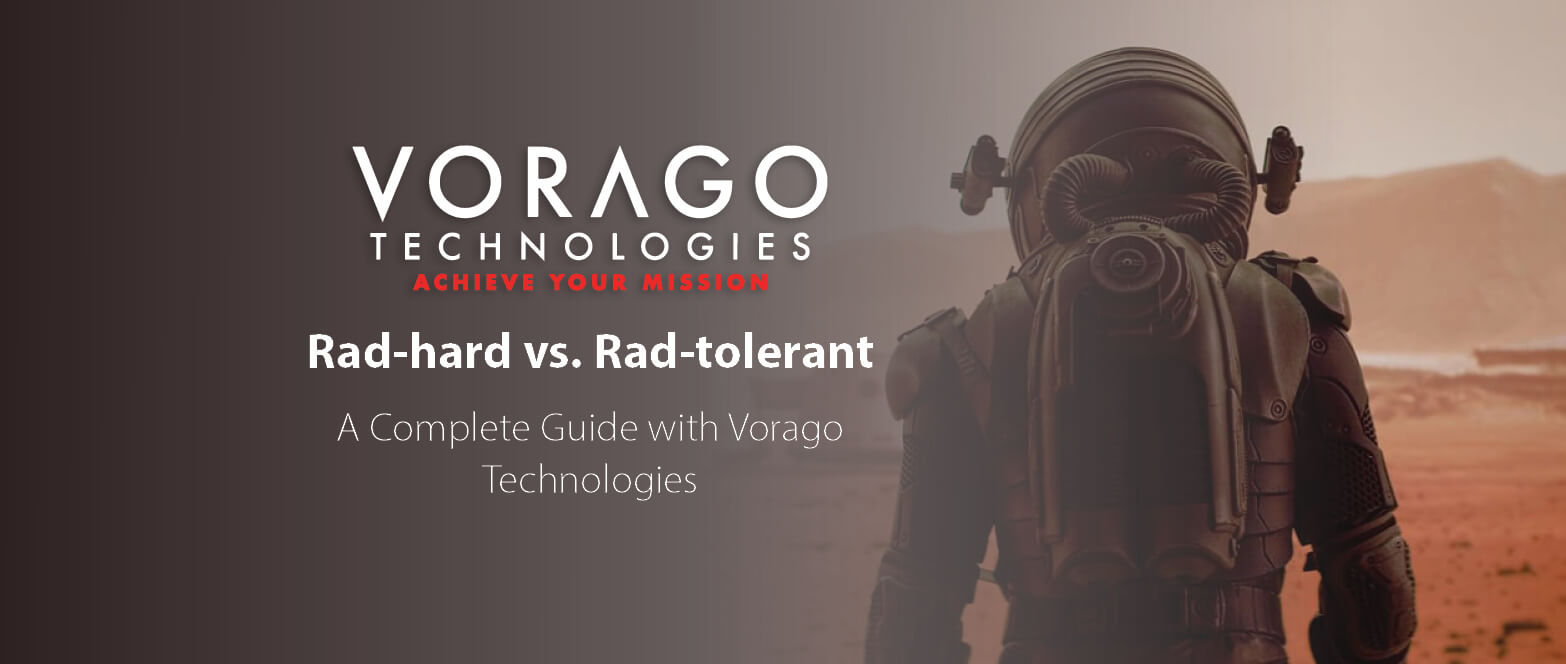
Rad-hard vs. Rad-tolerant: A Complete Guide with Vorago Technologies
Radiation damage poses a significant threat to electronics in the harsh environment of space. High radiation levels can cause catastrophic damage to electronic components. This can result in mission failure, financial losses totaling millions or billions of dollars and months or years of lost time. Aerospace engineers designing components for space missions can protect against these radiation effects by using a rad-hard MCU.
What is radiation-hardening?
Put simply, radiation hardening makes electronic components resistant to damage caused by radiation exposure. When you take an integrated circuit and put it in high radiation environments such as space, it is exposed to high energy radiation that passes through the semiconductor body. Some of the energy of the incident radiation is transferred into the semiconductor, creating mobile charge. The currents resulting from this charge can flow into circuit nodes which lead to circuit malfunction, either instantly or over time.
Radiation hardening is the process in which specialised techniques are used to create a semiconductor IC which is resistant to the effects of the resulting charge and currents so that energetic strikes on the circuit do not impact its functioning correctly.
Two prominent classes of radiation hardening are Radiation Hardening By Design (RHBD), which uses special design libraries and devices and Radiation Hardening By Process (RHBP), which often uses specialised, often expensive, semiconductor fabrication processes.
VORAGO’s patented HARDSIL® technology uses cost-effective, high-volume manufacturing to harden any commercially designed semiconductor component for extreme environment operations.
Definitions of Rad-hard vs Rad-tolerant
Radiation-hardened and radiation-tolerant components offer varying levels of radiation protection from high levels of ionizing radiation. The difference between rad-hard versus rad-tolerant is a matter of degree of robustness against or resistance to these radiation effects.
What are radiation tolerant electronics?
Radiation-tolerant electronics offer a middle ground between commercial components and radiation-hardened components. Rad-tolerant components can tolerate more radiation doses and/or fluxes than standard consumer electronics, but they tolerate lower radiation exposure than radiation hardened devices.
Usually, these parts were not purposefully made to be radiation-tolerant. They were typically made for another application, such as automotive or medical, but turned out to have a higher level of radiation tolerance which makes them useful for space applications.
Innovative rad-hard solutions that fit seamlessly into existing process and design flows
VORAGO's high-rel, high performance, rad hard VA41620 with HARDSIL® technology is designed to deliver mission success.


VORAGO Radiation-Hardened Arm® Cortex®-M4 - Highly capable MCU manufactured with HARDSIL® technology to help you achieve your mission
Levels of Radiation Protection
Rad-hard Radiation Protection
Radiation-hardened components are the gold standard for space missions and other applications involving extreme radiation doses. Rad-hard components protect against significant levels of radiation. Although there is no absolute guarantee, radiation-hardened parts help to ensure a very low chance of malfunction over the course of a mission.
Rad-tolerant Radiation Protection
Radiation-tolerant electronics are less sensitive to the passage of radiation than commercial electronics, but not nearly as resilient as their radiation-hardened counterparts. Importantly, there is no industry standard definition of “radiation-tolerant” – so some rad-tolerant parts offer substantially better radiation performance than commercial electronics, but others may not be much stronger than a commercial part.
Radiation energy thresholds and fluxes for instantaneous disturbance and cumulative doses before malfunction are all much lower with radiation-tolerant parts than radiation-hardened, so there’s a much higher chance of malfunction over the course of the mission.
How to Find a Reliable Manufacturer or Supplier
Testing and quality standards are more stringent for radiation-hardened components than for radiation-tolerant parts. Some components, such as QML parts, require extra testing above and beyond the basics for traditional radiation-hardened parts.
When a supplier tells you their part is radiation-hardened or radiation-tolerant, you want to understand exactly how they are getting to that determination. Inquire about their test methods, and which qualification standards they are following. Doing the upfront research to ensure you are getting the right components to meet the specialised requirements of your mission will save you time, money and headache. Reputable suppliers will expect and welcome these questions.
VORAGO Technologies is the only pure-play, Rad-hard Arm® company. For over 15 years, VORAGO have led the industry in providing radiation-hardened components and extreme-temperature solutions for Aerospace, Defence and Industrial projects around the globe.
Official distributors for VORAGO Rad-Hard MCU's - Available across Europe, UK and Ireland
APC works close with industry-leading Aerospace and Defence manufacturers to provide you with the largest selection of radiation-hardened components on the market, delivered faster and more cost-efficiently, giving you faster time-to-mission and reduced costs. Contact an expert today.
As AS9120B Certified distributors, our space-compatible technologies include, but are not limited to: Radiation-Tolerant, Semiconductors, Microelectronics and Optoelectronic Components, including Integrated Circuits. APC can also supply high-density ‘ System-in-Package ’ solutions that miniaturise radiation tolerant systems.
VORAGO is the only pure-play, Rad-hard Arm® company, providing radiation-hardened components for extreme environments. With a proven track record, including more than 30 flight badges, VORAGO is dedicated to emerging hardening technologies that will continue to evolve, providing the agility to achieve mission success — faster.